An Insight into the working of a 4 Stroke Internal Combustion Engine
- WG
- Dec 8, 2019
- 4 min read
Updated: Dec 8, 2019
We almost take our Internal Combustion Engines for granted, don’t we? All we do is buy our vehicles, hop in and drive around. There is, however, a history of development to know about. The compact, well-toned, powerful and surprisingly quiet engine that is purring under your vehicle’s hood just wasn’t the tame beast it seems to be now. It was loud, it used to roar and it used to be rather bulky. In fact, one of the very first engine designs to be conceived wasn’t even like the engine we know so well of today.

An internal combustion engine is defined as an engine in which the chemical energy of the fuel is released inside the engine and used directly for mechanical work, as opposed to an external combustion engine in which a separate combustor is used to burn the fuel.
The internal combustion engine was conceived and developed in the late 1800s. It has had a significant impact on society, and is considered one of the most significant inventions of the last century. For example, consider how this type of engine has transformed the transportation industry, allowing the invention and improvement of automobiles, trucks, airplanes and trains. Internal combustion engines can deliver power in the range from 0.01 kW to 20x103 kW, depending on their displacement. They complete in the market place with electric motors, gas turbines and steam engines. The major applications are in vehicles (automobile and truck), railroad, marine, aircraft, power stations and even households. The vast majority of internal combustion engines are produced for vehicular applications, requiring a power output on the order of 102 kW.
But, how do they work?
As difficult as it may seem, it is very intriguing to note that the engine works on one of the most basic concepts of Fluid Mechanics that we as students learn as part of our introductory course, i.e. the Ideal Gas Law, which implies that ‘the pressure of a given mass of gas varies directly with the absolute temperature of the gas and inversely to its volume under ideal conditions’ Mathematically it can be stated as:
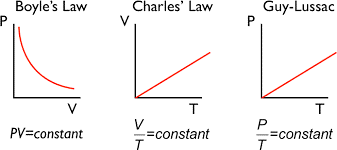
where P, V and T are pressure, volume and temperature of the gas respectively.

As we can see in the above figure, there are 4 cylinders in the engine which perform to and fro motion about an axis in which two cylinders go up and the other two go down simultaneously. This ensures that the total volume of the air-fuel mixture entered in the system remains constant. Now when the cylinders go up, pressure increases and so does the temperature and when the cylinders go down, pressure goes down and so does the temperature of the mixture.
The working can be summarized in four steps, namely:
1. Intake: Also known as induction or suction. This stroke of the piston begins at top dead center (T.D.C.) and ends at bottom dead center (B.D.C.). In this stroke the intake valve must be in the open position while the piston pulls an air-fuel mixture into the cylinder by producing vacuum pressure into the cylinder through its downward motion. The piston is moving down as air is being sucked in by the downward motion against the piston.
2. Compression: This stroke begins at B.D.C, or just at the end of the suction stroke, and ends at T.D.C. In this stroke the piston compresses the air-fuel mixture in preparation for ignition during the power stroke (below). Both the intake and exhaust valves are closed during this stage.
3. Combustion: Also known as power or ignition. This is the start of the second revolution of the four-stroke cycle. At this point the crankshaft has completed a full 360-degree revolution. While the piston is at T.D.C. (the end of the compression stroke) the compressed air-fuel mixture is ignited by the heat generated from high compression (diesel engines), forcefully returning the piston to B.D.C. This stroke produces mechanical work from the engine to turn the crankshaft.
4. Exhaust: Also known as outlet. During the exhaust stroke, the piston, once again, returns from B.D.C. to T.D.C. while the exhaust valve is open. This action expels the spent air-fuel mixture through the exhaust valve.
Our Model
We made a completely functional model of the ‘in-line’ 4 stroke internal combustion engine embarking upon its design and engineering principles, thermodynamic analysis, heat recovery, rod and piston to stroke ratio, energy balance, etc.
We made the model using four syringes which we cut as cylinders, some ice-cream sticks, a motor, straws (which represent the outlet and inlet pipes), and three pulleys that represent the gears that are present in the automobile.
We made it in such a way that two cylinder-shafts go up together and the other go down together so as to keep the volume of the air-fuel mixture constant and represent the four stages of the operation.
Here are some photos of our model:


Applications
Reciprocating piston engines are by far the most common power source for land and water vehicles, including automobiles, motorcycles, ships and to a lesser extent, locomotives (some are electrical but most use Diesel engines). Rotary engines of the Wankel design are used in some automobiles, aircraft and motorcycles.
Where high power-to-weight ratios are required, internal combustion engines appear in the form of combustion turbines or Wankel engines. Powered aircraft typically uses an ICE which may be a reciprocating engine. Airplanes can instead use jet engines and helicopters can instead employ turboshafts; both of which are types of turbines. In addition to providing propulsion, airliners may employ a separate ICE as an auxiliary power unit. Wankel engines are fitted to many unmanned aerial vehicles.


ICEs drive large electric generators that power electrical grids. They are found in the form of combustion turbines with a typical electrical output in the range of some 100 MW. Combined cycle power plants use the high temperature exhaust to boil and superheat water steam to run a steam turbine. Thus, the efficiency is higher because more energy is extracted from the fuel than what could be extracted by the combustion engine alone. Combined cycle power plants achieve efficiencies in the range of 50% to 60%. At a smaller scale, stationary engines like Gas engine or Diesel generators are used for backup or for providing electrical power to areas not connected to an electric grid.
(Sources of images used in this article: wikipedia, mrwaynesclass.com, ars.els-cdn.com, images.cdn.circlesix.co, miro.medium.com)
Written by B.Tech students Srijan Karn, Nikhil Musale, Tushar Jindal, Tanisha Agrawal and Swastik Dasgaonkar as part of their Fluid Mechanics lab project.
Comments